Investment in collaborative technology
Heathcoat Fabrics is excited to announce recent investments in advanced automation technologies, further solidifying our commitment to efficiency, quality and sustainability. This investment includes installing a collaborative robotic (Cobot) doffing system in our new production building within our yarn processing department (XTEX).
The new Cobot system automates the doffing of finished bobbins, loading of empty tubes and the automatic restart of winding spindles. This new technology is a game-changer for our manufacturing process, enhancing productivity and reducing the risk of human error. As a result, our skilled staff can focus on producing the complex texturised yarns that go into our award-winning products.
“We installed our first Cobot this summer, and we have already seen significant improvements in operational efficiency” – Peter Hill, Director of Woven Fabrics
Stepping up a gear in Yarn Processing
Collaborative robots are designed to integrate into workspaces shared with human co-workers. Compared to traditional industrial robots, they are easier to program and integrate as they do not require cages or guarding. Within our XTEX unit, the Cobot is taking on one of the most demanding and repetitive tasks in our yarn processing department, running 24/7 without the need for breaks, eliminating errors and improving production quality. Additional benefits include:
- Health & Safety – Eliminating manual handling in hot and humid conditions, the Cobot significantly reduces workplace fatigue.
- Minimised Training Time – Automation requires minimal training, an advantage in a high-turnover environment.
- Improved Quality – With near-zero mistakes, the Cobot ensures consistent quality and precision.
- Reduced Variability – Following a strict Standard Operating Procedure (SOP), the Cobot ensures every operation is performed identically, reducing inconsistencies.
- Increased Efficiency – Built for speed and accuracy, Cobots can complete tasks faster than human workers and can do so without breaks, reducing downtime and boosting overall production capacity.
- Protecting Equipment – Correct alignment and precise handling by the Cobot prevent accidental damage to equipment and materials.
To support this initial installation, Heathcoat Fabrics is exploring further investments in automation. Plans are in place for the potential installation of additional Cobots and Automated Guided Vehicles (AGVs) to move goods across our site. While automation presents unique challenges due to the historic nature of our site, which has evolved over hundreds of years, we are committed to overcoming these obstacles in pursuit of operational excellence. Our continued exploration into advanced robotics is just one way of ensuring that Heathcoat Fabrics remains at the forefront of innovation in textile manufacturing, delivering efficient processes and the highest quality products to our customers.
Explore Heathcoat’s range of manufacturing capabilities here.
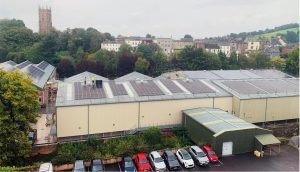
The new production building extending Heathcoat’s yarn texturising capacity and home to the latest collaborative robotic capability in our winding and covering area. The installation of a further solar array brings the solar PV total to 3,900 panels across our site.